Recognizing the Basics and Applications of Plastic Extrusion in Modern Manufacturing
In the world of modern-day production, the technique of plastic extrusion plays an important role. Deciphering the fundamentals of this procedure discloses the real convenience and capacity of plastic extrusion.
The Principles of Plastic Extrusion Process
While it may appear complicated, the principles of the plastic extrusion procedure are based on reasonably straightforward concepts. It is a production process in which plastic is thawed and after that shaped right into a continual account through a die. The raw plastic product, often in the form of pellets, is fed right into an extruder. Inside the extruder, the plastic is subjected to warm and stress, creating it to thaw. The liquified plastic is after that forced through a designed opening, called a die, to form a long, continual item. The extruded product is cooled and afterwards cut to the desired size. The plastic extrusion process is extensively made use of in various sectors due to its performance, cost-effectiveness, and adaptability.
Different Types of Plastic Extrusion Methods
Structure upon the basic understanding of the plastic extrusion process, it is essential to explore the numerous techniques entailed in this manufacturing approach. In contrast, sheet extrusion creates big, flat sheets of plastic, which are commonly more processed right into items such as food packaging, shower drapes, and cars and truck parts. Recognizing these techniques is key to making use of plastic extrusion successfully in modern manufacturing.
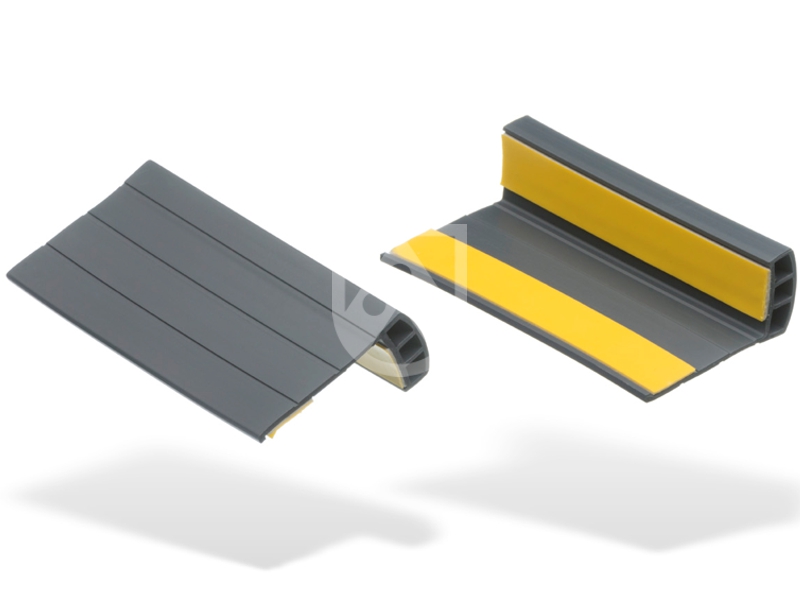
The Function of Plastic Extrusion in the Automotive Market
An overwhelming majority of parts in contemporary lorries are products of the plastic extrusion process. Plastic extrusion is primarily utilized in the production of different automobile elements such as bumpers, grills, door panels, and dashboard trim. Therefore, plastic extrusion plays a pivotal role in automotive manufacturing.
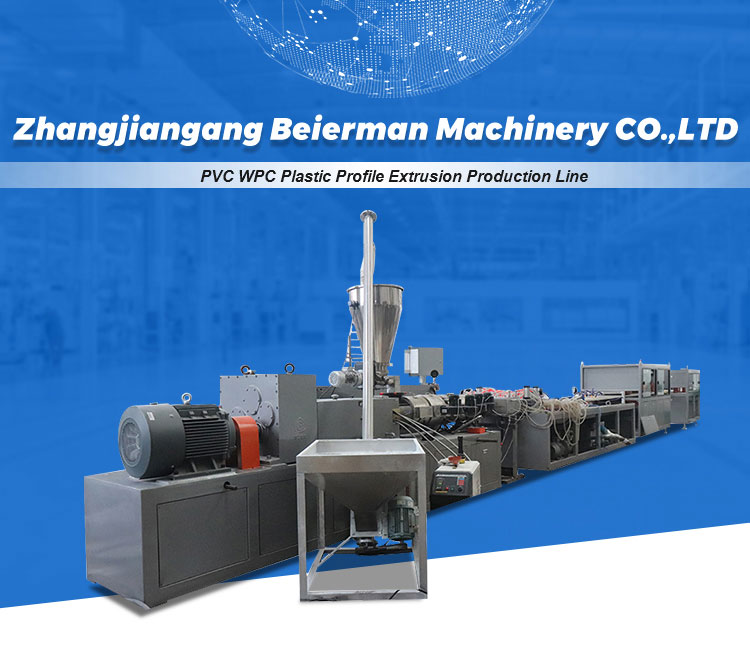
Applications of Plastic Extrusion in Customer Product Production
Beyond its considerable effect on the vehicle sector, plastic extrusion confirms just as reliable in the world of durable goods manufacturing. This process is essential in creating a wide array of items, from food packaging to household home appliances, toys, and also clinical devices. The flexibility of plastic extrusion enables producers to develop and produce intricate forms and sizes with high precision and effectiveness. Due to the recyclability of many plastics, click here now extruded components can be recycled, lowering waste and expense (plastic extrusion). The versatility, flexibility, and cost-effectiveness of plastic extrusion make it a recommended selection for many consumer items suppliers, contributing substantially to the industry's growth and development. The environmental ramifications of this prevalent use need cautious consideration, a topic to be discussed even more in the succeeding area.
Environmental Influence and Sustainability in Plastic Extrusion
The prevalent usage of plastic extrusion in manufacturing invites examination of its eco-friendly ramifications. As a procedure that regularly uses non-biodegradable materials, the environmental impact can be significant. Energy usage, waste manufacturing, and carbon discharges are all concerns. Sector improvements are increasing sustainability. Effective machinery reduces power use, while waste administration systems recycle scrap plastic, decreasing basic material needs. Furthermore, the development of eco-friendly plastics offers a more ecologically pleasant alternative. Regardless of these improvements, better development is required to alleviate the ecological footprint of plastic extrusion. As society leans towards sustainability, important source manufacturers must adjust to continue to be sensible, stressing the significance of constant study and development in this field.
Final thought
Finally, plastic extrusion plays a critical duty in modern production, particularly in the automobile and consumer goods markets. Its adaptability permits the production of a large range of components with high accuracy. Furthermore, its capacity for recycling and advancement of naturally degradable materials provides a promising opportunity towards sustainable practices, therefore dealing with environmental concerns. Understanding the essentials of this process is key to maximizing its benefits and applications.
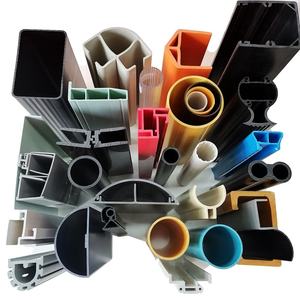
The plastic extrusion procedure is thoroughly made use of in different industries due to its adaptability, cost-effectiveness, and effectiveness.
Structure upon the fundamental understanding of the plastic extrusion process, it is necessary to check out the different methods included in this production technique. plastic extrusion. In contrast, sheet extrusion develops big, level sheets of plastic, which are commonly additional processed into products such see here as food packaging, shower drapes, and cars and truck components.An overwhelming majority of parts in modern-day vehicles are items of the plastic extrusion procedure